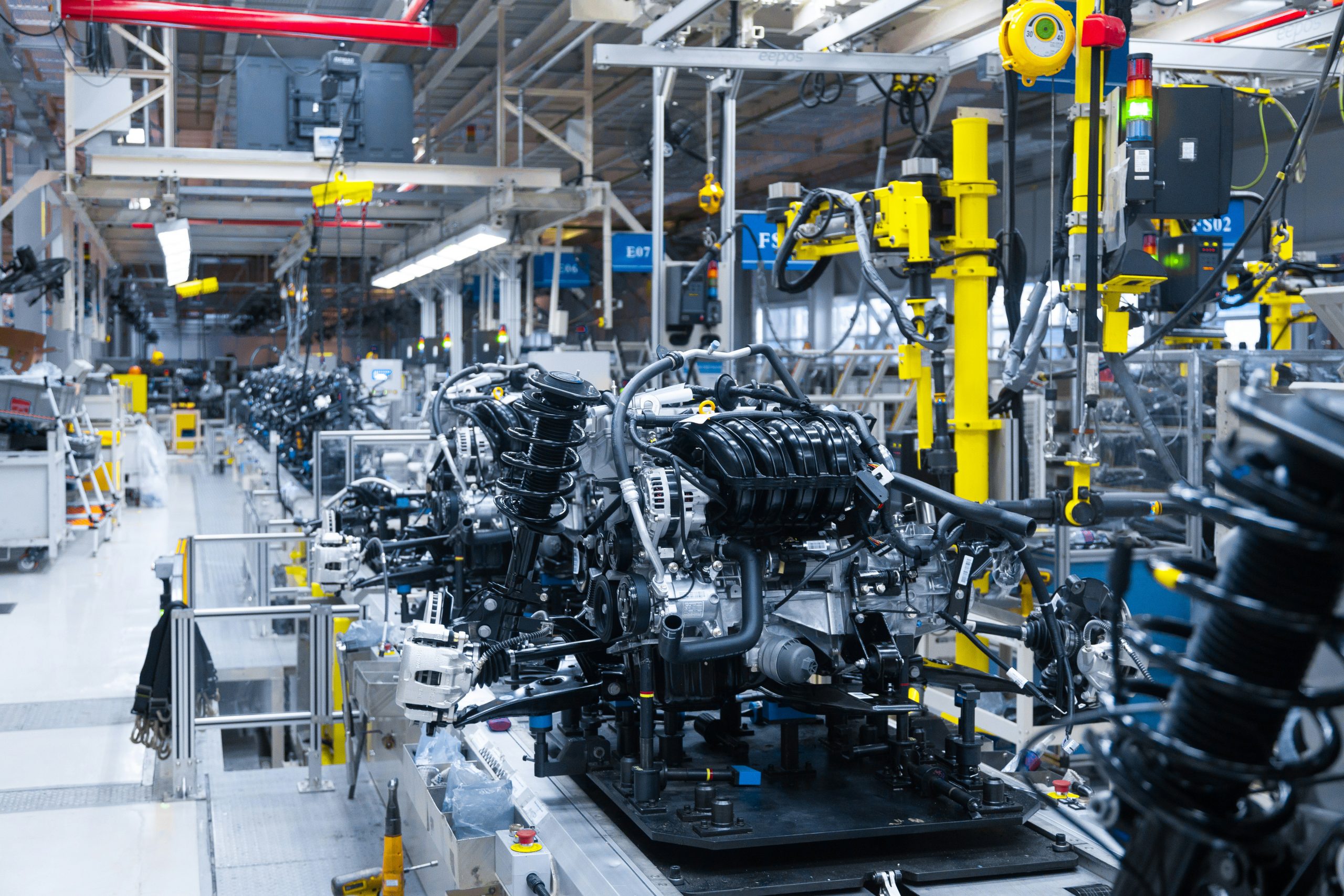
Mechanical engineering plays a vital role in the design and functionality of robots. As robotics advances, mechanical principles increasingly influence its development, allowing robots to perform tasks more efficiently and precisely. Mechanical engineers ensure that robots are built with the proper structural integrity, mobility, and control from industrial manufacturing to medical applications. This article explores how mechanical engineering applies its principles in robotics to create functional and reliable robots.
Kinematics and Dynamics in Robotics
Kinematics and dynamics are foundational mechanical engineering principles used extensively in robotics. It involves the study of motion without considering the forces that cause it, while dynamics deals with the forces and their impact on motion.
In robotics, kinematics is used to describe how robots move. For instance, the movement of robotic arms or legs can be studied using kinematic equations to determine the position, velocity, and acceleration of various robot parts. This knowledge helps engineers design robots with the correct range of motion needed for specific tasks.
Dynamic analysis is equally crucial in robotics. When designing a robot, engineers must consider how forces, such as torque or inertia, affect its movement. For example, when a robot arm lifts an object, dynamic analysis helps determine how much force is needed and how the robot will respond to varying loads.
By applying kinematics and dynamics, mechanical engineers ensure that robots can move smoothly and perform tasks efficiently. This principle is crucial in developing advanced robots, especially in manufacturing, space exploration, and healthcare environments.
Material Selection and Structural Design
The selection of materials for building robots is a critical aspect of mechanical engineering. Robots are subjected to various mechanical stresses, and the materials used must withstand these forces while maintaining lightness, strength, and durability. For example, materials used in a robot’s frame must be lightweight yet strong enough to support its weight and any additional load.
Common materials used in robotics include metals like aluminum and steel, which provide strength and durability. However, lighter materials, such as titanium and carbon fiber composites, are used when weight reduction is essential for the robot’s performance. Engineers also consider factors like corrosion resistance, flexibility, and ease of fabrication when choosing materials.
The structural design of a robot involves ensuring that its frame can handle mechanical loads without deforming. This is where mechanical principles like stress analysis come into play. Engineers calculate the stress distribution across various parts of the robot to ensure that each component will endure the forces it will encounter. Structural analysis helps prevent robot failures, especially in critical applications such as surgery or hazardous material handling.
Actuators and Power Transmission Systems
Actuators are a robot’s ” muscles” that convert energy into movement. They are central to a robot’s ability to interact with its environment. Mechanical engineering principles guide the design of actuators to ensure that they provide the right amount of force and speed for the intended task.
Various actuators are used in robotics, including electric motors, pneumatic actuators, and hydraulic actuators. Each has its advantages and limitations. Engineers commonly use electric motors because they are reliable, efficient, and easy to control. On the other hand, designers use pneumatic actuators in applications where space is limited because they offer high power density. Hydraulic actuators are robust and suitable for heavy-duty tasks but require a more complex power supply system.
Mechanical engineers also design power transmission systems, such as gears, belts, and pulleys, to transfer the energy actuators produce to the robot’s limbs or tools. These systems must be optimized to reduce energy loss and wear and tear. Gears convert rotational motion into linear motion, and their design must ensure smooth and precise operation.
Actuators and power transmission systems are key to a robot’s ability to perform tasks accurately and efficiently. By applying mechanical engineering principles, engineers ensure that robots have the necessary power and control to accomplish various functions, from assembly line operations to delicate surgical procedures.
Control Systems and Feedback Mechanisms
A robot’s control system ensures precise movements and task execution. Control systems use sensor feedback to adjust a robot’s actions in real time, requiring a deep understanding of mechanical and electrical engineering.
Mechanical engineers design robots with sensors that detect position, force, temperature, and other parameters. These sensors provide the necessary data to the robot’s control system, which uses algorithms to adjust the robot’s movements. For instance, a robot arm might have torque sensors that inform the control system if it applies too much force, preventing damage to the arm or the manipulated object.
Feedback mechanisms ensure that the robot operates within the desired parameters. For example, when a robot performs a repetitive task, like picking up an object, sensor feedback allows it to make real-time adjustments to maintain accuracy. This principle is fundamental in robotics applications requiring high precision, such as surgery or semiconductor manufacturing.
Mechanical engineers work closely with electrical engineers to integrate sensors and control systems into robot designs. This collaboration ensures that robots can function autonomously while maintaining high levels of safety and performance.
Automation and Human-Robot Interaction
Integrating mechanical engineering principles into robotics has facilitated the growth of automation across industries. Robots can now perform repetitive, dangerous, or complex tasks more efficiently than humans, reducing errors and increasing productivity. Automation in industries like manufacturing and logistics relies heavily on mechanical engineering to design robots that can work alongside humans or in hazardous environments.
Human-robot interaction (HRI) is another critical area of mechanical engineering. As robots are increasingly used in environments where they must interact with humans—such as hospitals, homes, or offices—designers must ensure they design robots to be safe, responsive, and easy to control.
Mechanical engineers focus on designing robots with ergonomic features that allow for easy interaction. For instance, robots that assist with caregiving must be safe to touch, easy to understand, and reliable in performing tasks. Additionally, designers often equip robots in industrial settings with safety features, such as collision detection and emergency stop functions, to protect human workers.