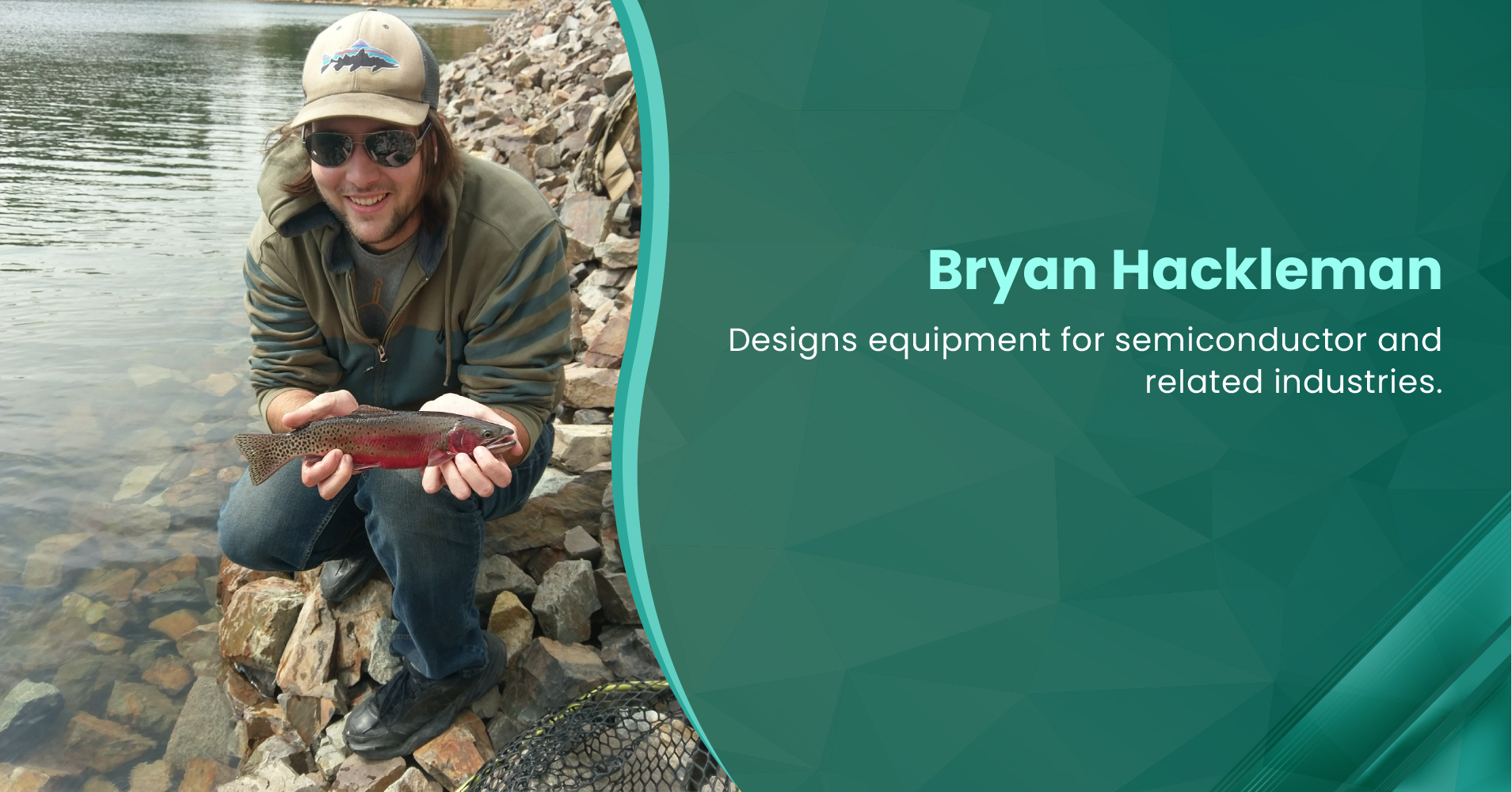
In chemical processing, catalysts play an essential role in enhancing the rate of chemical reactions without undergoing any permanent chemical change themselves. However, over time, catalysts can lose their efficacy due to factors such as fouling, poisoning, and thermal degradation. This can lead to decreased production efficiency, increased operational costs, and more frequent catalyst replacements. To mitigate these issues, optimizing the life cycle of catalysts through effective regeneration techniques is crucial.
Understanding Catalyst Deactivation
Before delving into regeneration methods, it is essential to understand the reasons behind catalyst deactivation. A variety of mechanisms can deactivate catalysts:
Fouling: Accumulation of heavy organic compounds or particulates on the catalyst surface, which block active sites.
Poisoning is the adsorption of impurities such as sulfur, phosphorus, or heavy metals that chemically interact with the catalyst, rendering it inactive.
Thermal Degradation: High temperatures can alter the catalyst’s physical structure, often leading to sintering or loss of surface area.
Recognizing the specific mode of deactivation is pivotal as it determines the appropriate regeneration strategy to be employed.
Regeneration Techniques
Effective regeneration of catalysts can restore their activity and extend their operational life, thus reducing the need for costly replacements. The following are some of the key techniques used in catalyst regeneration:
Thermal Regeneration: Thermal regeneration involves heating the catalyst in a controlled environment to burn off the accumulated contaminants. This method is particularly effective for catalysts fouled by organic compounds. Care must be taken to control the temperature to avoid further thermal degradation. In some cases, an inert or reducing atmosphere is used to prevent the catalyst’s oxidation.
Chemical Regeneration: When specific chemical compounds poison catalysts, targeted chemical treatments can be employed to remove these poisons. For instance, chemical agents can be used to dissolve metal contaminants or convert them into volatile compounds that can be easily removed. This method requires precise knowledge of the chemistry involved in both the poisoning and regeneration processes.
Wet Oxidation: Wet oxidation is a process in which the catalyst is treated with a combination of high temperature and pressure in the presence of oxygen and water. This technique is effective in removing organic fouls and some types of metallic poisons. It is also beneficial for regenerating catalysts used in liquid-phase processes.
Biological Regeneration: Emerging as a novel approach, biological regeneration involves using microorganisms to remove organic contaminants from catalysts. This method is considered environmentally friendly and can be effective at lower temperatures compared to thermal techniques.
Implementing a Regeneration Strategy
Implementing an effective catalyst regeneration strategy requires a systematic approach:
Diagnosis: Regular monitoring and analysis of catalyst performance to determine the onset and nature of deactivation.
Selection of Regeneration Method: The most appropriate regeneration technique is chosen based on the type of deactivation and the specific catalyst system.
Optimization: Fine-tuning the regeneration conditions, such as temperature, duration, and chemical agents, to maximize efficacy while minimizing damage to the catalyst.
Integration: Designing operational protocols that integrate regeneration cycles into the regular operation of the process to minimize downtime and disruption.
Benefits of Effective Catalyst Regeneration
Optimizing catalyst regeneration not only extends the life of the catalyst but also enhances the overall efficiency of the chemical process. Key benefits include:
Cost Reduction: Decreased need for new catalysts and reduced operational costs associated with downtime and less efficient processing.
Environmental Impact: Waste reduction associated with disposing of spent catalysts and decreased emissions from the process due to maintained catalyst efficiency.
Production Efficiency: Consistent product quality and output by maintaining catalyst performance at optimal levels.
Challenges and Future Directions
While regeneration can significantly extend the life of a catalyst, it is not always a panacea. Some catalysts may undergo irreversible deactivation that current regeneration techniques cannot remedy. Furthermore, the development of more robust catalysts that can withstand harsher conditions or are less susceptible to poisoning and fouling is an ongoing area of research.
Effective catalyst regeneration is a vital aspect of modern chemical processing, offering significant economic and environmental benefits. Advances in this field will continue to enhance the sustainability and efficiency of industrial operations, reflecting an integration of scientific innovation with practical application.